Trioplast testimonial for “Total Certified Renewable Polymers“
“As a leading producer of polyethylene film, we at Trioplast take responsibility for the environment in everything we do. We strive to reduce the amount of material in our products, we recycle waste materials and we continuously develop our expertise as to decrease our use of non-renewable raw materials. In short: We design solutions for the future.
Our growing sustainability portfolio consists of 3 product brands, each representing a different sustainable technology: TrioLoop (products based on recycled materials), TrioLean (products based on downgauged material) and TrioGreen (products based on biobased materials). As an additional service, we also offer TrioGreenway, a high quality package of Life Cycle Analysis customized to our customers needs in order to see the benefits and impacts for environment and economics.
Our vision is to reach zero carbon footprint and a minimal general environmental impact in our division and with our films. Of course, this cannot be obtained without a close collaboration with our raw material suppliers and customers. Therefore, the new stretch hood film from renewable certified polymers of Total is the first in the world made out of bio-allocated material.
As of September 2019, the Trioplast production plant in Nyborg, Denmark, is certified according to the international ISCC (International Sustainability & Carbon Certification) PLUS standards. This certification confirms that we are contributing to responsible sourcing of bio-allocated feedstock and enables us to produce a stretch hood film which is based to 100% on bio material made out of plant oil instead of relying on fossil sources. “This big step makes us one of the leading innovators in our industry in terms of sustainability”, says Laila Dallal, Sustainability Manager at Trioplast. “With this product in our portfolio, we have enhanced our range of environmentally friendly products, leaving a choice to the customer depending on his preferences”.
This true innovation brings film performance which is exactly the same as films from products made using materials based on fossil feedstocks. “It is safe to say that the TrioGreen Super Stretch is in no way different than existing products in terms of haptic, performance and properties”, states Jan Teglgaard, Product Manager for Stretch Hood & FFS films at Trioplast. “This is exciting for both Trioplast and our customers so we can contribute to a cleaner environment without compromising on performance or quality”.
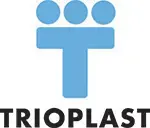
Nadja Herfurth, Head of Strategy & Product Management at Trioplast Industrial Film